I've run a topping lift line for a whisker pole. I would like to have a dedicated place to tie off the line on the mast when it is in use.
It doesn't make sense to run it back to the cockpit, as I will be forward messing with whisker pole any time I need to manipulate the line.
I think @Christian Williams had a similar cleat on Thelonious/Makana:
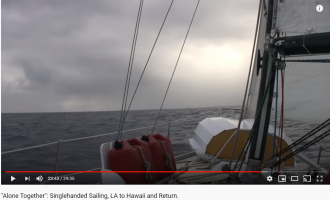
I'm looking for suggestions on the best way to attach such a cleat to the thin wall of my mast.
A few similar threads around on other sites:
jeanneau.proboards.com
Has anyone used "Rivnuts" ?
forums.ybw.com
This guy uses some sort of sleeved connector to attach a clutch to his mast.
He certainly has experience with various penetrations if his earlobes are any guide.
Should I just drill and tap the largest diameter machine screw that will fit through the holes in whatever cleat I buy?
Thank you for any suggestions.
It doesn't make sense to run it back to the cockpit, as I will be forward messing with whisker pole any time I need to manipulate the line.
I think @Christian Williams had a similar cleat on Thelonious/Makana:
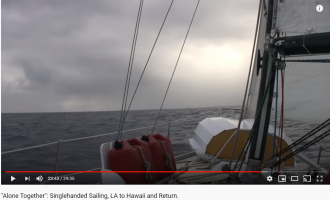
I'm looking for suggestions on the best way to attach such a cleat to the thin wall of my mast.
A few similar threads around on other sites:
Adding a Mast Cleat - Cruisers & Sailing Forums
OK. The furling genny halyard takes up one clutch on the piano, somewhat uselessly. I got a hold of a suitable cleat and am contemplating attaching to the port side of the mast , securing the halyard
www.cruisersforum.com
Attaching a cleat to the mast | Jeanneau Owners Forum
i am looking to replace small cleats on my mast used for lazy jacks with larger ones. My first thought was to drill and tap the mast for machine screws to attach the cleats. When I went
Has anyone used "Rivnuts" ?
Rivnuts in mast - which type?
I intend to mount an extra cleat on my mast, and have decided to use rivnuts. The cleat will be mounted with M6 s/s socket head set screws. The question I have is this. Do I use s/s rivnuts with plenty of chromate paste in the mast or aluminium rivnuts and rely on chromate paste on the...
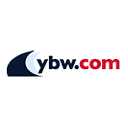
This guy uses some sort of sleeved connector to attach a clutch to his mast.
He certainly has experience with various penetrations if his earlobes are any guide.
Should I just drill and tap the largest diameter machine screw that will fit through the holes in whatever cleat I buy?
Thank you for any suggestions.