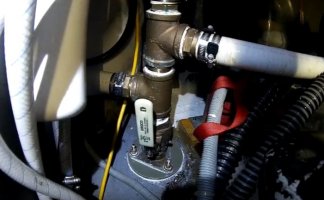
https://youtu.be/IorGAu0yhdk
I took this video in 3-5 foot seas, winds to 15 knots on a dead run, approximately 300 miles east of Kauai. The hull flex shown here is located directly beneath the forward area of the cockpit, just under the bridge deck. Note that the through-hull, flange, valve, and T-fittings are all new Groco parts installed in April 2016, or 2 months before this video was taken. The flange is through-bolted to the hull at three points, and the backing plate is made from a 5.5" round 3/8" thick G-10 sheet. The bronze bolt heads on the outside are countersunk and sealed in epoxy. No leaks were noted here during the transit from LA to Kauai, or about 2,200 miles. Biggest seas on this transit were 10-15' for 48 hours during the first leg of this transit (prior to the video being taken) The assembly replaces the original installed by Ericson, which was just a through-hull screwed directly into a valve, supported by a plywood backing plate with a lock nut, along with the two additional T-fittings: one for the galley sink, the other for the starboard scupper in the footwell behind the wheel. After observing this flex, this is one upgrade I'm glad to have made (both sides).
There's theory, and then there's the cold reality of watching this in a seaway. Watching this, I knew that FRP and that our hulls are meant to flex, and that all boats have some degree of flex. Take for example, this video of this steel container ship: https://www.youtube.com/watch?v=PmlTk_3NN_g. I also knew that the hull-to-deck joint is completely glassed together on the E35-II, further strengthening the whole boat. During the transit, I made it an almost daily routine to inspect bulkhead tabbing, the hull-to-deck joint where practical to inspect, chain plate attachment points on bulkheads, the ability to open and close locker and head doors, evidence of gel coat crazing in the liners and floor pan, and anything else that would indicate that attention would be needed. I also inspected the rudder tube, gland, and post, the quadrant and steering cables....all sorts of things. I saw nothing out of the ordinary...no cracking of FRP, no crazing gel coat, no bulkhead separation.
One additional note: The engine cover on my E35-II is located under the dinette...great access to the engine. With the hull flex shown in the video, the wooden engine cover produced enormous amounts of noise as it rubbed against the FRP floor pan, which is NOT bonded to the hull on these early boats...the floor pan just sits on top of plywood stringers below it that are bonded to the hull. The most interesting thing about this wasn't the noise necessarily. It was that, when I removed the engine cover, it was nearly complete silence in the cabin. You'd hear the occasional crackle of wooden furniture or bulkheads here and there, but the silence was in sharp contrast to the noise produced by the engine cover. I took all this evidence (especially the silence in the cabin) to mean that the boat was operating well within the design limits in the sea state I was in, and that the hull flex was simply also part of the design. Separate and apart from that, however, she somehow seems "more loose" after that voyage...not sure if it's always been there and I'm just now noticing it because of the amount of time I just spent in my boat, or if it's something new from having crossed 2,200 miles of open ocean.
Not necessarily a question here, but thought I'd post this for observations/comment.
Last edited: