After having been told that you can't really steam bend kiln dried teak, I approached this project with trepidation given the recent price hikes of the material (see my previous post). I have been slowly working my way forward on my E31 with finishing out the trim, and now am doing the difficult (curvy) parts. This piece goes in the head.

Laying out for templates
As many of you know, there are no straight lines on a boat, and in many cases compound curves abound such as this piece I am fitting.
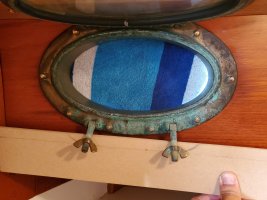
Templating in 1/8 inch mdf. Turns out I don't need to clearance for the dogs on the port.
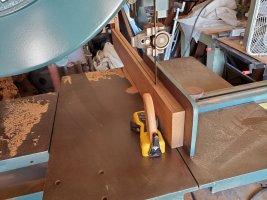
Resawing teak blank to ballpark thickness on my band saw.
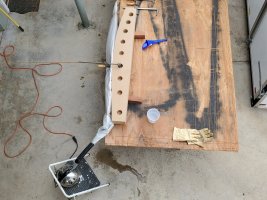
Instead of building a steam box, I am trying out the steam in place method popularized
by Lou Sauzedde. The form is mdf and is shaped to account for some spring back. The
bag is custom made from 6 mil plastic.
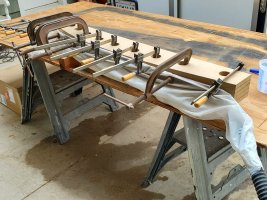
Here we go, all clamped up and cooking. The thickness is about 5/8 inch and I
cooked it well over an hour and left it to cool on the form overnight. The next day
I took it off, and the springback was about what I expected.
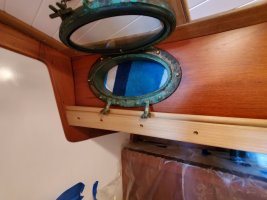
And here it is screwed and glued. Again, because it's a boat, compound miters were
needed on both ends.
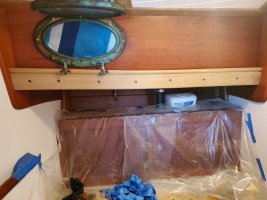
Here's another view. Pardon the distortion but it's shot with a cell phone.
So this was a successful shallow bend of kiln dried stock. The real test
will come next when making the piece up forward that curves through about 160 degrees.
Stay tuned.

Laying out for templates
As many of you know, there are no straight lines on a boat, and in many cases compound curves abound such as this piece I am fitting.
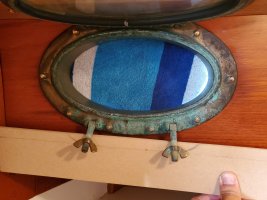
Templating in 1/8 inch mdf. Turns out I don't need to clearance for the dogs on the port.
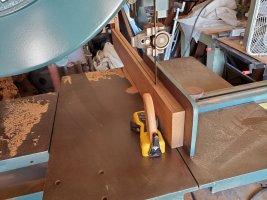
Resawing teak blank to ballpark thickness on my band saw.
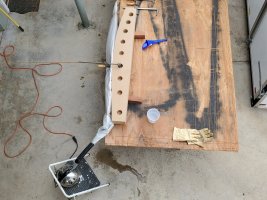
Instead of building a steam box, I am trying out the steam in place method popularized
by Lou Sauzedde. The form is mdf and is shaped to account for some spring back. The
bag is custom made from 6 mil plastic.
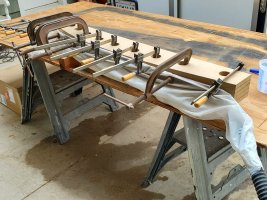
Here we go, all clamped up and cooking. The thickness is about 5/8 inch and I
cooked it well over an hour and left it to cool on the form overnight. The next day
I took it off, and the springback was about what I expected.
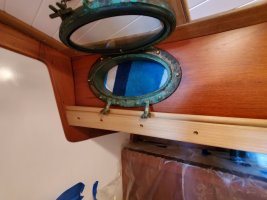
And here it is screwed and glued. Again, because it's a boat, compound miters were
needed on both ends.
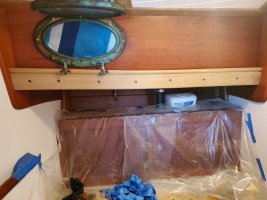
Here's another view. Pardon the distortion but it's shot with a cell phone.
So this was a successful shallow bend of kiln dried stock. The real test
will come next when making the piece up forward that curves through about 160 degrees.
Stay tuned.